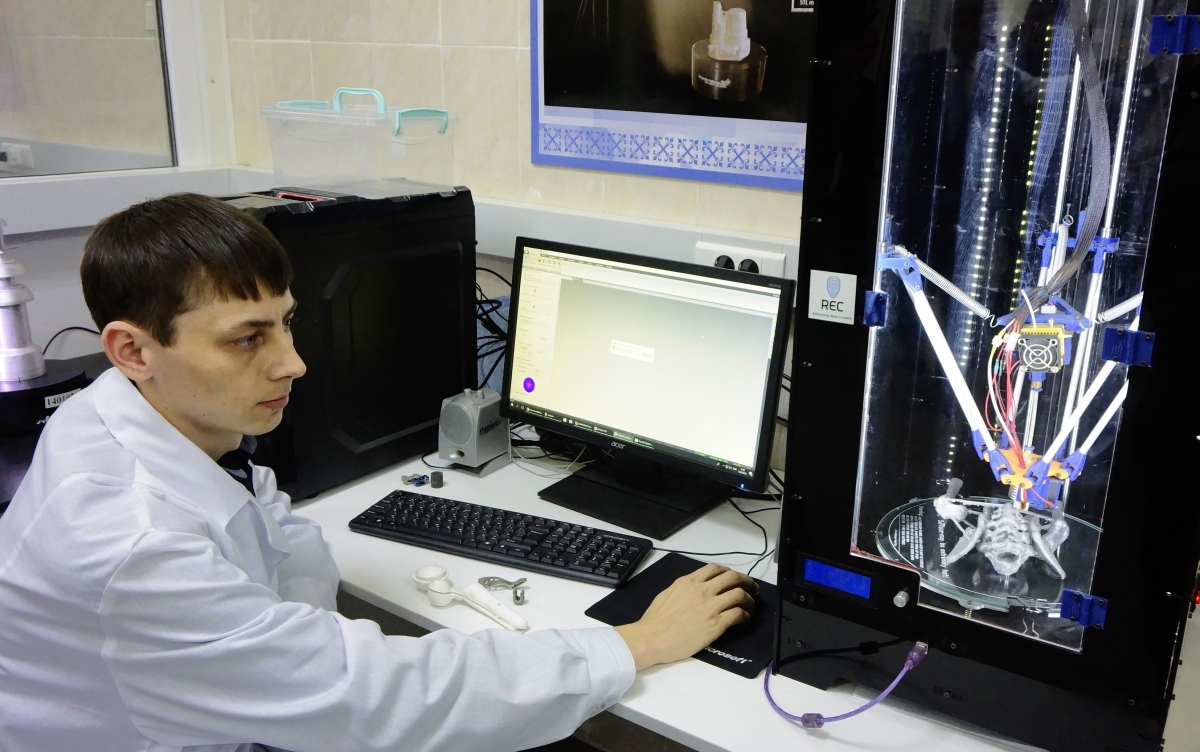
«Казахстанская правда» уже рассказывала о научных проектах, в которых используются выпускаемые в Восточном Казахстане металлы («Титан на службе у здоровья» от 20.07.2017 года и «Металл элитный, марки Grade» от 30.01.2018 года).
Как сообщили в АО «Усть-Каменогорский титано-магниевый комбинат» (УК ТМК), металл для производства изделий медицинского назначения был получен в результате инновационного проекта по выпуску титановых слитков и сплавов методом вакуумно-дуговой плавки, успешно реализованного комбинатом в 2010 году в рамках Государственной программы форсированного индустриально-инновационного развития (ГП ФИИР).
Продукция цеха вакуумно-дуговой плавки является продукцией с высокой добавленной стоимостью четвертого технологического передела и применяется в авиакосмической, нефтегазовой отраслях, атомной энергетике, оборонной промышленности.
Благодаря своим уникальным свойствам – биологической совместимости с тканями человеческого тела – титан также широко используется для изготовления спинных имплантов, эндопротезов суставов, элементов для лечения переломов. В связи с этим начиная с 2010 года АО «УКТМК» наладило производство и экспорт в Западную Европу специальных медицинских титановых сплавов Grade 5 марки Еli.
Для дальнейшего развития титано-магниевого производства с учетом перспективного направления рынка по применению титана в медицине флагман титановой отрасли выразил заинтересованность в научно-технической поддержке проекта по выпуску имплантов и протезов со стороны профильных вузов Казахстана.
В соответствии с научно-целевой программой ВКГТУ по развитию НИОКР, согласованной с УК ТМК, в рамках проекта «Выпуск титановой продукции для дальнейшего использования в медицине» осуществлена разработка технико-экономического обоснования по производству биоимплантов и медицинских инструментов из титана и его сплавов без применения метода титанового напыления деталей.
Теперь – слово за уполномоченными контролирующими органами, ведь для начала выпуска новой медицинской продукции необходимо прежде всего наличие государственных стандартов по производству имплантов из титана, системы их лицензирования и сертификации. В Казахстане вышеупомянутые нормы и институты в настоящее время отсутствуют.
В свою очередь, ученые ВКГТУ им. Д. Серикбаева предложили технологию печати имплантов на 3D-принтере по металлу. Кроме того, здесь разработали метод нанесения напыления из тантала, а также титана на изделия медицинского назначения.
Сегодня в университете от исследований и проб перешли к испытанию образцов. Как рассказал проректор по науке и международному сотрудничеству ВКГТУ Олег Гавриленко, республиканский научно-исследовательский институт травматологии и ортопедии предоставил свои разработки, на основе которых с помощью 3D-печати в университете изготовили прототип межтелового кейджа для позвоночника. Образно говоря, это шайба, которую имплантируют, чтобы срастить позвонки.
Сами операции известны и освоены еще с 40-х годов прошлого века. Меняются только хирургические технологии, конструкции и кейджи – материал, из которого изготовлены импланты. В Усть-Каменогорске использовали сплав титана, ниобия и тантала, предоставленного АО «Ульбинский металлургический завод» (УМЗ).
– Сплав тантала, титана и ниобия получен на нашем промышленном оборудовании, – рассказал директор танталового производства УМЗ Алексей Цораев. – На данный момент нигде в мире он не используется для выпуска имплантов. Университет сейчас тестирует металл, исследует его свойства. Наша задача – получить материал, совместимый с костной тканью.
Первыми, кому вживят «таблетку» Ti-Nb-Ta, будут кролики. По словам руководителя проекта профессора университета Сергея Плотникова, в течение 3 месяцев в Новосибирске и Астане в специализированных НИИ возьмут под наблюдение несколько подопытных животных. Затем у них исследуют кровь – выделяются ли вредные вещества. И проверят ткани – нет ли омертвения, или, иначе говоря, отторжения. В случае если результат на биосовместимость окажется положительным, сплав может открыть для завода новую производственную нишу.
Другим изделием, выполненным в партнерстве со столичным НИИ травматологии и ортопедии, стала головка эндопротеза тазобедренного сустава. Этот имплант используется при лечении такой довольно распространенной травмы, как перелом шейки бедра. К сожалению, бывает, что покрытие эндопротезов негативно влияет на хрящевую ткань сустава, изнашивает ее. Поэтому производители медицинских изделий постоянно конкурируют в поиске новых материалов и конструкций.
Усть-каменогорский образец смоделирован в 3D-проекции, изготовлен на токарном станке с числовым программным управлением и имеет два слоя лазерного напыления. Первый слой – титан, второй – гидроксиапатит – минерал, являющийся главным компонентом зубной эмали и костной ткани человека. Дальше образец для протезирования должен получить заключение медиков.
С областью медицины связан также проект изготовления сверхпроводника для магниторезонансного томографа. Сам провод – разработка УМЗ. Наука помогает заводу протестировать его механические и физические свойства на испытательной машине. В течение года, по словам руководителя танталового производства, на УМЗ разработают технико-экономическое обоснование.
– Конкуренция на этом рынке жесткая, никто нас там не ждет, – дал комментарий Алексей Цораев. – На данном этапе анализы, которые мы можем сделать самостоятельно, показывают, что образцы нашей продукции соответствуют мировому уровню. Самым серьезным является вопрос цены. Мы должны оценить степень нашей конкурентоспособности и необходимые объемы производства. За счет крупнотоннажного выпуска можно достичь хорошей себестоимости, но потребуются дополнительные работы по новым видам материалов. Мы надеемся на господдержку, без нее направления, связанные с медициной, тяжело поднять. Сейчас вся работа ведется за счет собственных сил, без покупки какого-либо оборудования. Но чтобы наладить большое и надежное производство, нужен госзаказ.