Степногорский завод занимает лидирующие позиции среди родственных предприятий стран Содружества
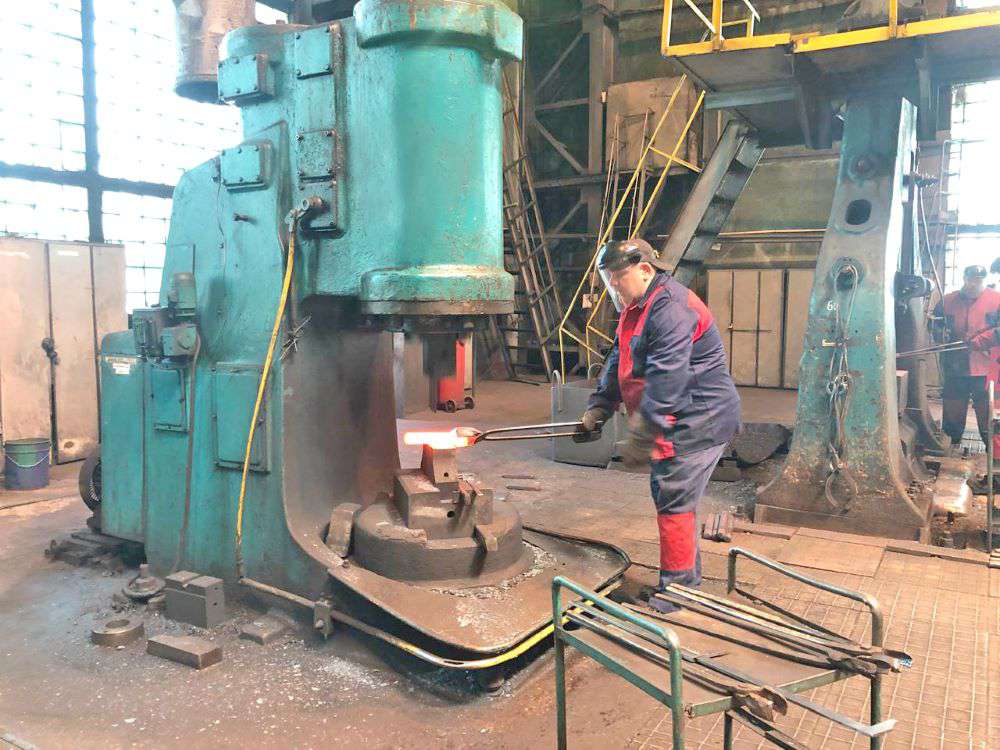
Масштабы поражают воображение
Степногорский подшипниковый завод – одно из старейших предприятий региона, которое специализируется на выпуске подшипников для железнодорожных, горнодобывающих, металлургических и химических производств. Его история началась в 1972 году, когда в окрестностях молодого промышленного города начали расти корпуса будущего мощного предприятия. В декабре 1977-го тут выпустили первый подшипник. Эту дату и принято считать официальным днем рождения сегодняшнего СТПЗ.
Того, кто впервые оказывается в АО «СТПЗ», поражают прежде всего масштабы: завод раскинулся на 32 гектарах в производственной зоне Степногорска. В центре огромного комплекса из нескольких цехов находится бытовой корпус, включающий техническую библиотеку, радиостудию, раздевалки, душевые, столовую, спортивные залы.
Впечатляет и технологическое оснащение завода, уровень культуры производства, порядок на рабочих местах. Благодаря современному оборудованию, высокой квалификации персонала здесь выпускают надежную продукцию, рассчитанную на работу в любых климатических зонах.
По словам генерального директора завода Алексея Кукушкина, их изделия востребованы не только в нашей стране. Около 85% подшипников уходит на экспорт, Казахстан забирает примерно 15% объемов товара в месяц, при этом завод полностью покрывает внутренние потребности республики.
География поставок охватывает страны ЕАЭС, Европу и Африку. В 2023 году предприятие прошло европейскую сертификацию по стандарту EN 12080, получив допуск к эксплуатации на железных дорогах Евросоюза. Для организации поставок открыты офисы СТПЗ в Германии и Польше.
Серьезные суммы регулярно вкладываются в модернизацию производства. К примеру, в 2024-м на эти цели было инвестировано 2 млрд тенге. В текущем году в рамках новой инвестиционной программы на обновление и развитие производства намечено направить еще около 1,5 млрд.
Сегодня товарная линейка изделий предприятия включает семь типовых вагонных подшипников, 25 модификаций локомотивных, 80 типов сферических, 106 цилиндрических, шесть типов подшипников с витым роликом и другие.
Начали производить и один тип буксового сдвоенного подшипника, имеющего ряд конкурентных преимуществ перед обычными. Металл для изделий приобретается в Казахстане и Китае. Интересно, что новые типы подшипников разрабатываются прямо на месте усилиями собственной конструкторской службы.
Мощность завода составляет более 2 млн изделий в год. В 2024-м выпущено 1 млн 616 подшипников, в марте нынешнего года выдан 52-миллионный подшипник.
На сегодня в АО «СТПЗ» ежемесячно производят в среднем 100 тыс. подшипников. На заводе трудятся 2 500 человек.
От заготовок
до готового изделия
Предприятие уникально тем, что здесь налажен полный цикл производства. Рождение важной детали, без которой техника не поедет и не полетит, начинается с грохота штамповочной машины и завершается нанесением логотипа. Весь процесс происходит в шести основных заводских цехах, каждый из которых играет важную роль в общей технологической цепочке.
Первый шаг – штамповка заготовок. Затем они поступают на токарную и термическую обработку, а после шлифуются. В литейно-сепараторном цехе, где трудятся 99 человек, выпускают каркас подшипника. Начальник цеха Дмитрий Корбмахер показывает современное оборудование: здесь и корейские термопласт-автоматы, и американские фрезерные станки, и китайская техника с числовым программным управлением (ЧПУ).
Возглавляемая Олегом Ададимовым служба инструментального производства занимается выпуском инструментов и технологической оснастки. В этом подразделении трудятся 155 рабочих и 33 специалиста инженерно-технического состава. Среди них токари, фрезеровщики, шлифовщики, а также редкие на сегодня профессионалы, такие как заточник, аппаратчик азотирования, лекальщик, наплавщик. Поскольку подготовку таких специалистов сейчас не осуществляют, но они заводу нужны, их обучение проводят прямо на производстве.
На участке сферической оснастки за токарным станком с ЧПУ «колдует» токарь Алексей Володин. Он изготавливает штуцеры, ниппели, матрицы. Прежде чем запустить агрегат, сам составляет управляющую программу, налаживает оборудование и только потом нажимает на кнопку «Старт».
– Такую сложную геометрию, как сейчас, вручную уже не сделаешь, теперь без ЧПУ никак, – говорит он.
В другой зоне цеха восемь рабочих заняты изготовлением металлических заготовок для производства методом ковки. Здесь пышет жаром раскаленный докрасна металл. Специальности рабочих говорят сами за себя: кузнец-штамповщик, машинист молота, нагревальщик металла. Это тяжелый, но очень важный труд.
Начальник кузнечно-штамповочного цеха Евгений Грачев рассказывает, что на этом участке производятся заготовки наружных и внутренних металлических колец – всего около 78 наименований продукции весом от 3 до 40 килограммов. Работа ведется на современном японском оборудовании Аmada.
На участке высокого давления, который входит в состав службы главного механика, в этом году установлены новые насосы. Главный механик Сергей Головастиков называет эту зону «сердцем» всего кузнечно-штамповочного цеха. Обновление продолжается: помимо новых насосов введен в работу компрессор с увеличенным ресурсом.
Сборка подшипников – предпоследний этап, перед тем как они, упакованные в коробки, отправятся на склад. Здесь уже нет никаких роботов – только руки опытных мастеров. Именно они вручную соединяют все элементы – ролики, кольца, сепараторы. Собранные изделия аккуратно плывут по конвейеру на участок контрольного замера радиального зазора.
Изделия, прошедшие контроль, отправляются на маркировку и финальную сборку. Внутреннее кольцо соединятся с блоком – и подшипник готов! Изделия укладываются в коробки, маркируются и порой прямо со склада загружаются в вагоны для отправки заказчикам.
На страже качества
Не просто важное, а стратегическое место в производственном процессе занимает лабораторная служба предприятия, которой уже многие годы доверяют по всей республике и за ее пределами.
По словам начальника комплексно-метрологической лаборатории Лилии Онисько, в их подразделении проводят поверку и калибровку средств измерений, применяемых на производстве при контроле выпускаемой продукции.
В лаборатории механических испытаний проверяют на прочность пластмассу и металл. Немецкое оборудование спектральной лаборатории ЦЗЛ позволяет анализировать химический состав сталей, цветных металлов и сплавов. По словам ее начальника Татьяны Зубаревой, они могут выдавать и экспертные заключения.
Инженер-технолог Фархат Кумаков работает в центральной заводской лаборатории четыре года. Его основная функция – обеспечение производства качественными технологическими составами, другая важная часть работы – контроль качества полиамидного сепаратора для подшипника экспортного исполнения.
Артур Войцехович – инженер-металлофизик центральной заводской лаборатории. Одна из его производственных задач – количественное определение структурных составляющих подшипниковых сталей методом рентгеноструктурного анализа на дифрактометре POWDIX 600.
Разумеется, завод живет не только производственными достижениями. Здесь берегут, хранят и передают традиции, создавая атмосферу преемственности и уважения к труду. Особое внимание уделяют социальной составляющей.
На предприятии работает собственное радио, издается газета «Движение». Почти 15 лет назад создан музей – не просто выставка, а настоящее хранилище истории завода, его людей, передовиков производства, составляющих тот самый золотой фонд.
В экспозиции представлены образцы подшипников. Вход в музей оформлен в виде полуарки, стилизованной под подшипник.
Сегодня в АО «СТПЗ» трудятся около 40 рабочих династий, продолжая дело, начатое первыми поколениями заводчан.