Отслужившие срок рефрижераторы превращаются в термовагоны
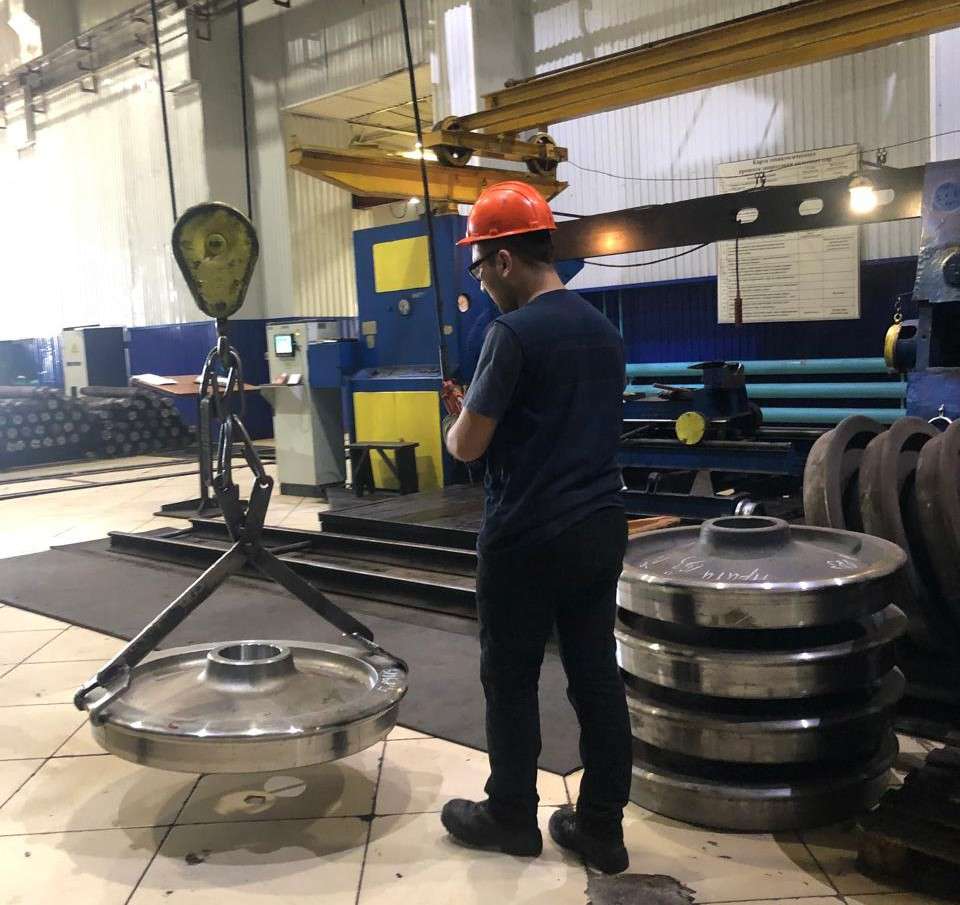
В ТОО «Вагонно-ремонтное депо «Бурабай» ремонтируют подвижной состав не только со всей республики. Сюда обращаются владельцы грузовых вагонов из России, других стран СНГ. Дело в том, что, помимо соотношения разумных цен и надежного качества ремонта, ТОО из Щучинска – пока единственное в Казахстане предприятие, получившее официальное разрешение на модернизацию рефрижераторов и превращение их в так называемые термовагоны.
В нынешнем году одно из старейших отраслевых предприятий области отмечает 90-летие. Его история началась в 1935 году с ремонтного пункта для грузовых вагонов. Через 13 лет он расширился до вагонного депо.
В середине 80-х годов прошлого века здесь провели масштабную реконструкцию: обновили производственные цеха, построили новое административно-бытовое здание. Большим событием для коллектива стало открытие в 1995-м вагонно-колесных мастерских (ВКМ). Пять лет спустя по производственным соображениям депо разделили на два самостоятельных участка – ремонтный и эксплуатационный. В 2001-м на базе ремонтного подразделения было создано ТОО «Вагонно-ремонтное депо «Бурабай».
По рабочим цехам нас сопровождает и. о. главного инженера товарищества Дархан Балтабай. Молодой человек начинал здесь токарем, а со временем вырос до руководящей должности.
– Основное наше направление – ремонт грузовых вагонов, деповской и капитальный, а также заводской ремонт колесных пар, – рассказывает специалист. – С 2008 года в ТОО начали осваивать более сложные виды работ: капитальный ремонт с продлением срока службы универсальных платформ, которые переоборудуются под перевозку большегрузных контейнеров, хоппер-дозаторов, а также крытых вагонов и зерновозов. Освоили непростую, требующую особой точности задачу, такую как деповской ремонт цельнометаллических пассажирских вагонов. Все это стало возможным, конечно же, благодаря постепенному оснащению вагонно-ремонтного депо «Бурабай» современным станочным, диагностическим оборудованием, грузоподъемными механизмами и компьютерной техникой.
По словам Дархана Балтабая, труд на предприятии автоматизирован на 90%. Однако, к примеру, подбор подшипников при сборке колесных пар проводится только вручную. Причем к этой ответственной работе допускаются лишь опытные слесари пятого разряда, которые ежегодно проходят аттестацию.
У ремонтников внушительные производственные мощности: ежегодно деповскую наладку здесь проходят до 2 400 вагонов, еще 240 – капитальную. В колесном цехе заводским ремонтом восстанавливают до девяти тысяч колесных пар.
Ремонтная база депо – это пять основных цехов под одной крышей. К примеру, в вагоносборочном ремонтируют железнодорожный подвижной состав, в частности тормозное оборудование, кузова, рамы и крыши вагонов.
В тележечном цехе выполняют наладку деталей тележек грузовых вагонов, восстанавливают надрессорные балки и боковые рамы. В механическом изготавливают запчасти, детали для ремонта вагонов. Свои функции выполняют автосцепное отделение, автоконтрольный пункт, столярно-хозяйственный и другие отделения.
Заходим в вагонно-колесные мастерские, куда относится и колесно-роликовый цех. Здесь выполняется важная работа, которая на профессиональной терминологии называется «обыкновенное освидетельствование, полное освидетельствование буксовых узлов колесных пар, а также заводской ремонт со сменой элементов нового формирования колесных пар».
Старший мастер цеха по ремонту колесных пар Юрий Агафонов посвятил предприятию 32 года. О вагонах и их колесах он, пожалуй, знает все, поскольку начинал когда-то с осмотрщика, дойдя до должности одного из ключевых специалистов. Под его началом трудятся 74 человека, большинство из них – молодые люди. Новичков обучают прямо на производстве.
По словам Юрия Анатольевича, часть рабочих станков, надежных и высокоточных, удалось сохранить еще с советской поры. В нынешнем году один из таких – карусельный станок для расточки колесных центров по внутреннему диаметру – прошел капитальный ремонт и модернизацию. За ним работает самый молодой токарь предприятия – Галым Хайруллов. «Молодец, быстро научился!» – отзывается о парне старший мастер цеха.
Давно заменен в депо на электронную систему и бумажный самописец для контроля качества запрессовки колесных пар. Вся информация о произведенном процессе теперь заносится в компьютер, где хранится в течение 25 лет. На экране прибора отображается график давления, напоминающий электрокардиограмму: каждый импульс соответствует определенному уровню усилия запрессовки. Однако механический самописец как резервное средство контроля убирать все же не стали. «На всякий случай», – улыбается Юрий Агафонов.
К слову, для обеспечения производственных цехов сжатым воздухом на предприятии имеется собственное компрессорное отделение.
Чтобы оставаться конкурентоспособными на стремительно развивающемся рынке ремонта вагонов (в Казахстане, по словам специалистов, родственных предприятий на сегодня насчитывается около 20), в вагоноремонтном депо «Бурабай» постоянно ищут и внедряют современные технологии и системы управления.
Кроме того, ТОО обладает государственными лицензиями на сбор, хранение, переработку лома, отходов цветных, черных металлов и сбыт их юридическим лицам. Есть у товарищества и разрешение на ремонт подъемных сооружений.
Как и в любой стабильно действующей компании, в ТОО «ВРД «Бурабай» делают ставку на кадры. На сегодня здесь трудятся 323 специалиста. Для сотрудников созданы необходимые условия: работают столовая, медпункт, спортзал с тренажерами, имеется прачечная для стирки спецодежды. На предприятии планомерно и последовательно занимаются улучшением социальной составляющей как дополнительным весомым стимулом для сотрудников.
Отметим, что здесь ежегодно проводят индексацию зарплаты. Кроме того, ко Дню железнодорожника, Дню Независимости работники поощряются премиями в размере двух окладов.